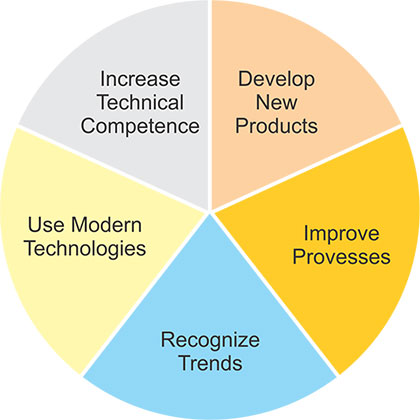
The Research and Development Sector (R&D) makes a wide contribution to enhancing performance in the production plants, to improving quality in all company sectors and to ensuring our production processes are environmentally sound. Work is also carried out on the new Taalay Metallics.
The R&D topics are as varied as our products and processes. We work not only in the metal recovery sector, recycling and extracting by-products, but also in metal refining in the form of wire, cast shapes and strips. The R&D team consists of specialists in the metallurgy, chemistry and process technology sectors.
To complement our own resources, we also work with other research facilities on project work related to special topics. The R&D structure is tailor-made to suit the different companies and their requirements. Additional members of the R&D staff are at the main subsidiaries where they are responsible for special development activities. They are therefore able to work on process improvements or products directly on site.
Product Development
The R&D assignments in the copper product sector are varied and growing. For example, the team is concentrating on improving the quality of strips and on the new development of special products − important projects to secure our leading position in the copper market. In addition, the product range is enhanced in the oxygen-free and low-alloyed wire and shape sectors. Products are developed in collaboration with customers with defined conductivity, strength and workability. In the process we learn the materials' basic parameters and likewise gain knowledge about casting properties. Both represent important basic information for the production side.
Process Development
The further development of production processes increases productivity in our production plants and Taalay’s earnings. The best possible utilization of resources, high process stability and environmental friendliness are our targets.
We use modern technologies for process analysis and monitoring to improve process control. Specially adapted sensors are often necessary due to the rough conditions in our furnaces. With the aid of the aforementioned technologies we optimize metal production in the furnace and converter as regards throughput and processing time.
But not only modern process control brings better results. Optimization work in our processes’ metallurgy and chemistry sectors also saves costs, reduces the process complexity of the production chain and increases product quality and environmental friendliness.